Make your first
support-free part
Due to our tailored hatching strategies you will be able to manufacture support-free parts and save build time and total costs.
Satellite Tank (support-free overhangs down to 20°)
Machine: SLM®500
Material: Ti64
This use case represents a satellite tank that is printed support-free. The overhangs go down to 20°. In comparison, using conventional data-preparation the inner area of the satellite need to be supported and would have been not removable afterwards.
Satellite Tank (support-free overhangs down to 30°)
Machine: SLM®500
Material: Ti64
This use case represents a satellite tank that is printed support-free. The overhangs go down to 30°. In comparison, using conventional data-preparation the inner area of the satellite need to be supported and would have been not removable afterwards.
Closed impeller (support-free overhangs down to 25°)
Machine: SLM®500
Material: Ti64
An impeller is a propeller enclosed in an annular or tubular housing.
This sample demonstrates the potentials to reduce support volume and to manufacture impellers with closed hosing due to simulation-based hatching strategies in GENESIS. As a result, the blades inside the impeller were printed with a good surface without supports. With conventional data-preparation the blades must be supported. In a real case with the closed housing, the support structures could not be removed from the inner area of the impeller.
Impeller demonstrator (support-free vs. supported blades)
Machine: SLM®280; Aconity Midi; GE ConceptLaser
Material: Ti64 and steel 316
An impeller is a propeller enclosed in an annular or tubular housing. For demonstration purposes, a part of the impeller housing has been cut free in order to make generated supports on the individual blades visible.
The blades in one half of the impeller were supported in a conventional manner using the pin supports. In another half of the impeller, the blades were supported only in the bottom area. The major surface of blades in this half of the impeller is support-free. The both halves of the impeller are manufactured with the same process parameters.
This sample demonstrates the potentials to reduce support volume and to manufacture impellers with closed hosing. In a real case with the closed housing, the support structures could not be removed from the inner area of the impeller.
The similar impellers with the same geometry were successfully manufactured from different materials (Ti64 and steel 316) on different machines (SLM 280, Aconity, GE ConceptLaser).
Impeller (support-free overhangs down to 20°)
Machine: SLM®280
Material: Ti64
A manufactured part is an impeller with exposed blades. All blades, cooling channels inside the outer walls and the hollow inner area of the impeller are manufactured without support structures. The support-free overhangs are down to 20°. Thus, the support structures are avoided in the areas, where the removal of the support material would be impossible.
Hip joint implant (support-free inner area)
Machine: SLM®280
Material: Ti64
This implant is an acetabular cup with integrated lattice structures. The fine details across the geometry of the acetabular cups are needed to create osseointegration, the optimal connection between the implant and the bone.
Conventional software defines the hatching strategy based on a purely geometric approach and generally supports the overhanging areas of the component with an overhang angle between 0 ° and 45 °. By using GENESIS supports in the inner area of the hip joint were dispensed entirely.
MINIMIZE YOUR
SUPPORT STRUCTURES
While support structures can be dispensed with entirely in certain applications, in many other cases the support structures are unavoidable, especially for the overhangs in the range between 0° and 20°. The following components demonstrate, how the support structures can be reduced with the use GENESIS software.
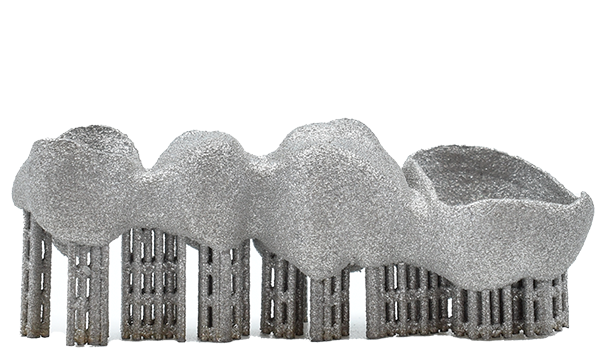
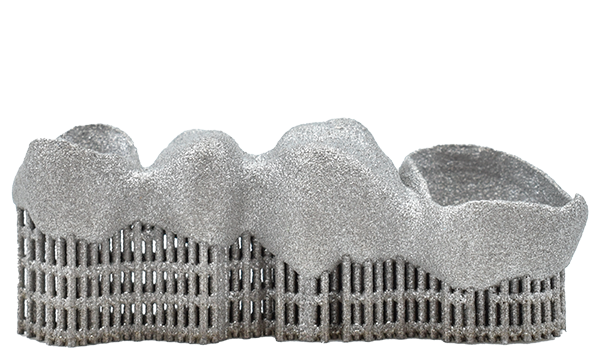
Small Denture
Machine: SLM®280
Material: Ti64
Partial dentures need to fit the patient without any compromise resulting in very individual geometries. 3D-printing offers a cost efficient and precise manufacturing method for the dental industry.
With GENESIS we were able to avoid the support structures for overhangs in the range from 45° to 15°. The result was a significant reduction of the support volume. This leads to a corresponding reduction of manual work for the removal of supports and saves costs by mass production of dental parts.
Dental Bridge
Machine: SLM®280
Material: Ti64
This dental bridge offers another example of significant reduction of the support volume. Over 40% support volume was saved compared to conventional part preparation.
Minimized support volume leads to reduced post-processes and overall manufacturing costs.
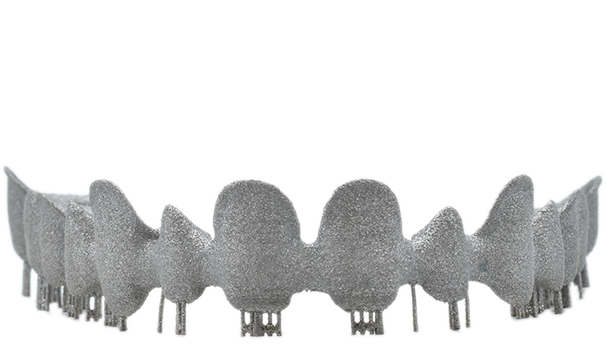
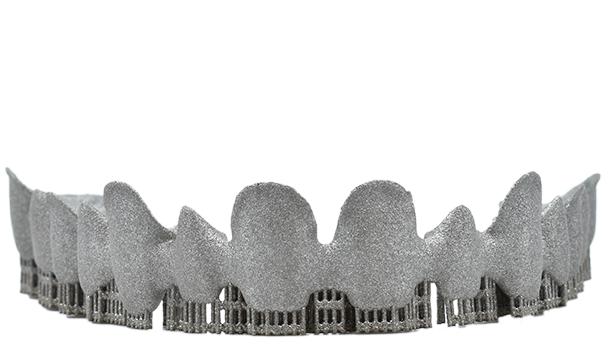
INCREASE YOUR
COST EFFICIENCY
By using GENESIS you can reduce support volume, build and post-processing time and therefore the total manufacturing costs.
Check out following cases for further details.
Conventional part preparation
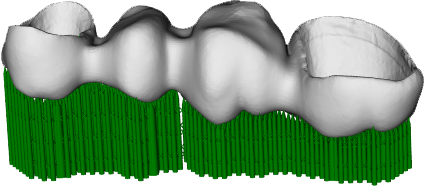
Initial situation
Supported overhangs: 0° - 45 ° Hatching Strategy: Conventional
Part preparation using GENESIS
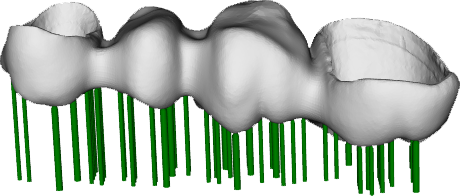
GENESIS preparation
Supported overhangs: 0° - 15 °
Hatching Strategy: Simulation-based
Conventional part preparation
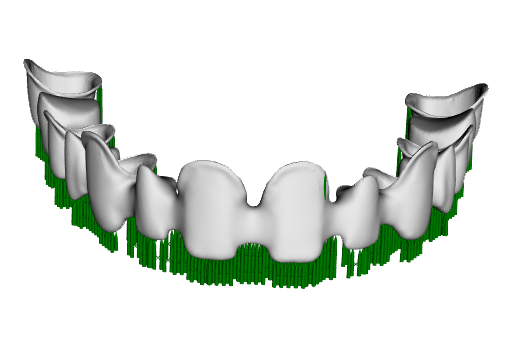
Initial situation
Supported overhangs: 0° - 45 ° Hatching Strategy: Conventional
Part preparation using GENESIS
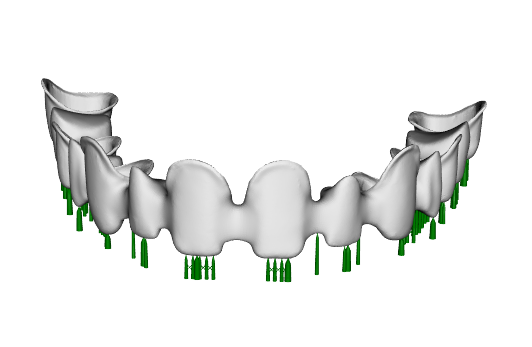
GENESIS preparation
Supported overhangs: 0° - 15 °
Hatching Strategy: Simulation-based
Conventional part preparation
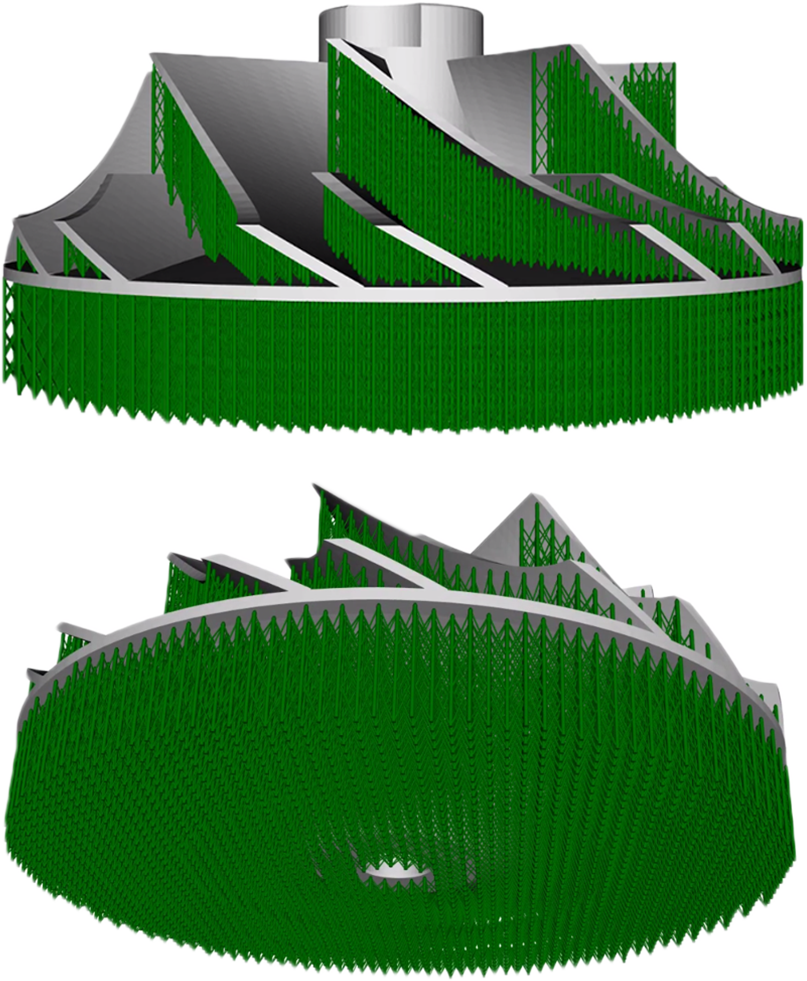
Initial situation
Supported overhangs: 0° - 45 ° Hatching Strategy: Conventional
Part preparation using GENESIS
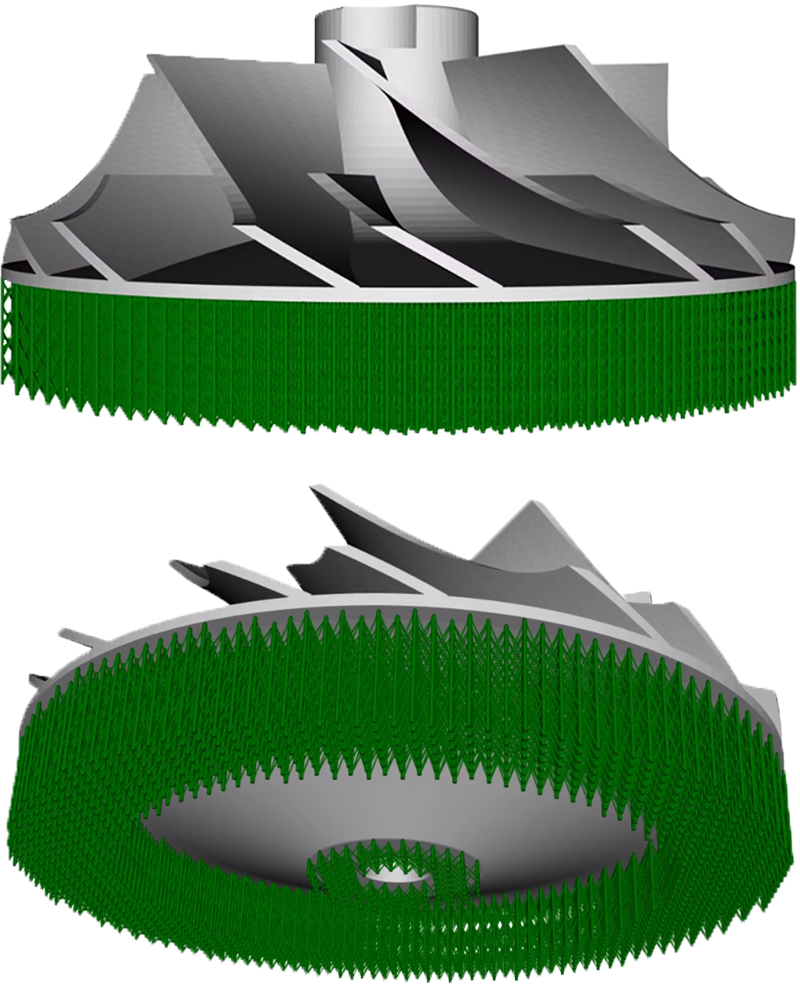
GENESIS preparation
Supported overhangs: 0° - 15 °
Hatching Strategy: Simulation-based