Products
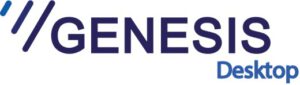
for
End-Users
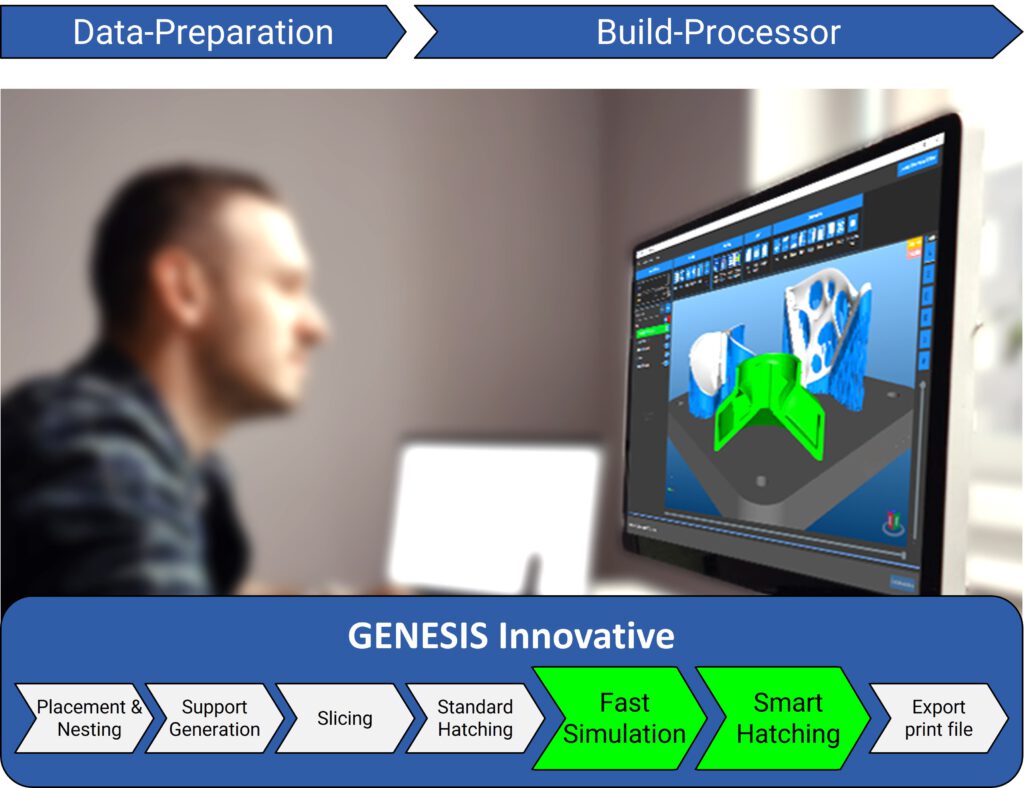
- Desktop software
- Data-Preparation including a Build-Processor
- Two options:
- GENESIS Innovative – Smart Hatching
- GENESIS Classic – Standard Hatching
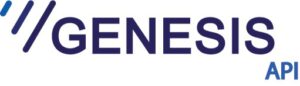
for
LB-PBF System Vendors
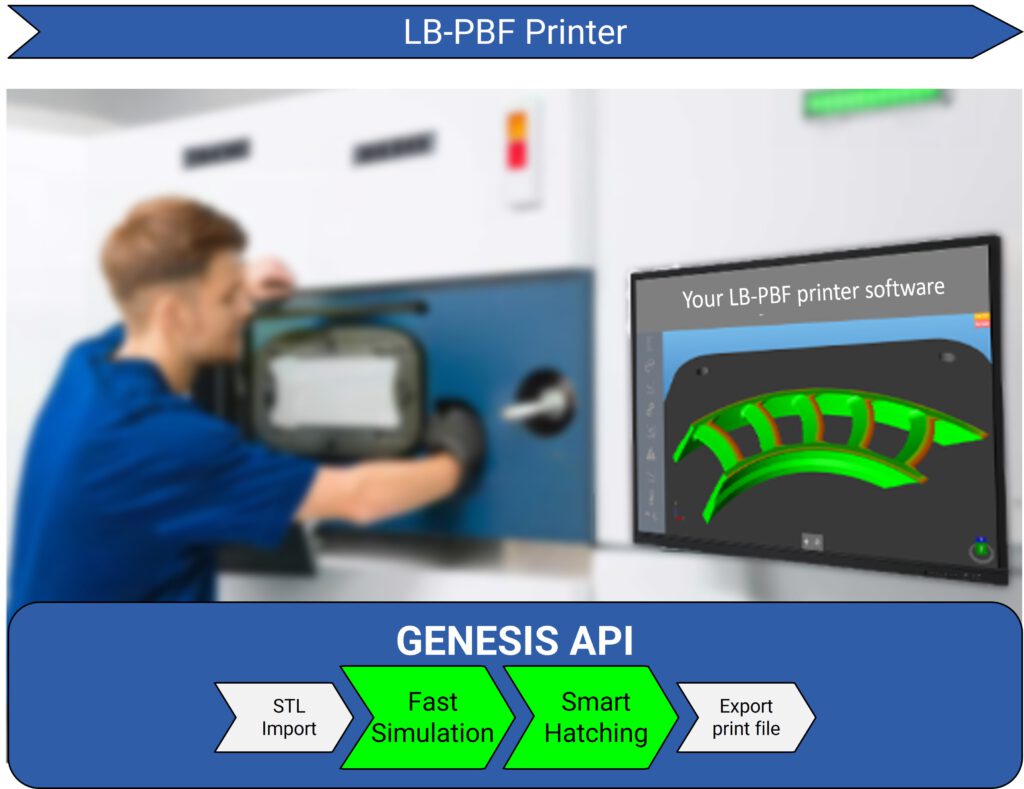
- Build-Processor as API package
- For integration into LB-PBF system software
- API package:
- Fast simulation of overheating
- Smart Hatching incl. parameter adaption
GENESIS Desktop
for End-User
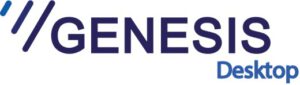
available in two options - Innovative or Classic
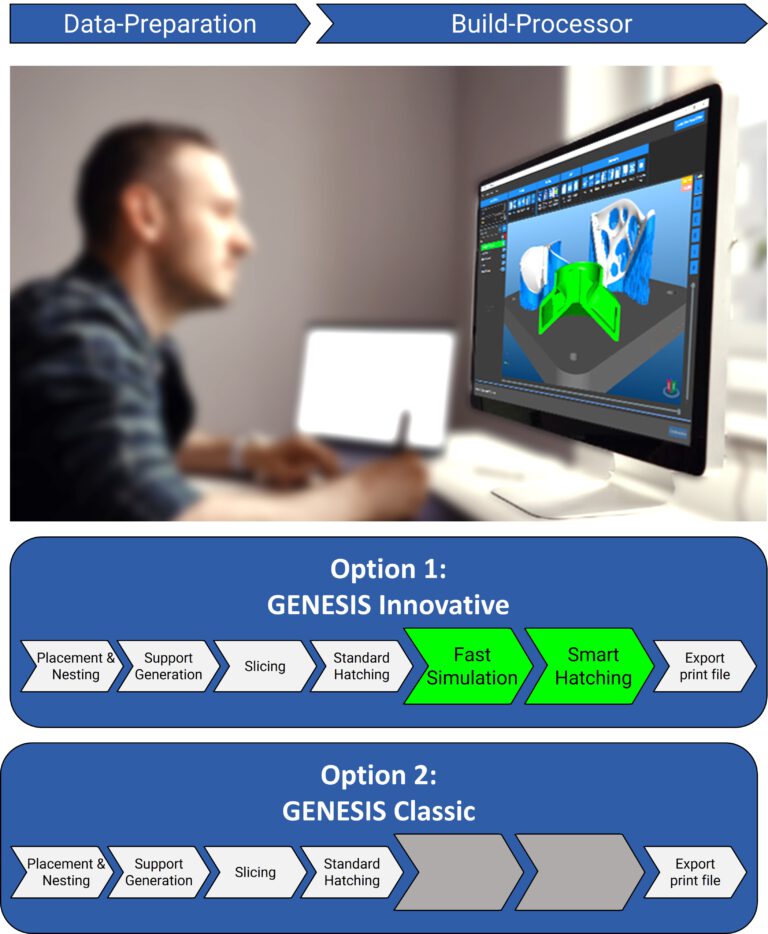
Innovative Features
Fast Simulation of overheating
- Fast simulation of overheating within seconds for small parts and minutes for big parts
- Automatic detection of overheated zones based on material, process parameter and geometric specialties
- The color gradient in the video from green to red represents the criticality level for overheating
- Red areas represent an increased risk of overheating
Smart Hatching incl. parameter adaption
- Simulation-based optimization of hatch orientation and sequence in areas with high risk of overheating
- Precise simulation-based parameter adaption in areas with high risk of overheating
- Two parameter adaption modes:
- Hatch-wise adaption – one parameter per hatch
- In-Hatch-wise adaption – multiple parameters within one hatch
- Improves the thermal management during printing
- Reduces distortion during printing
- Lowers the risk of recoater collision during printing
Classic Features
Placement
- Import of any part and corresponding support structure in the common .stl file format
- Move parts
- Rotate parts
- Scale parts
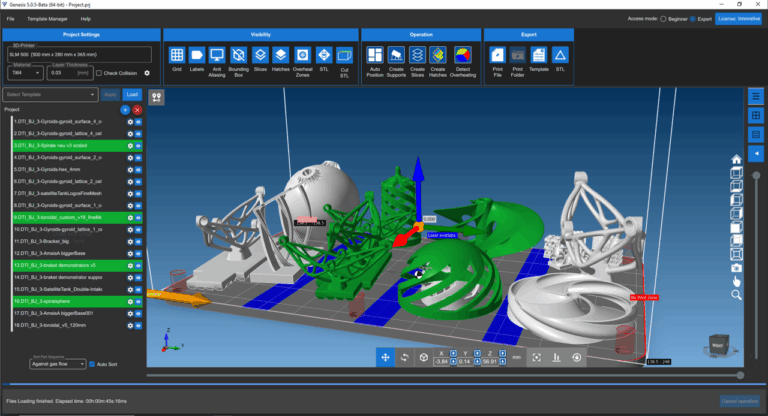
Nesting
- Automatic smart placement and orientation of parts
- Consider gasflos and recoater directions to minimize buildjob failures
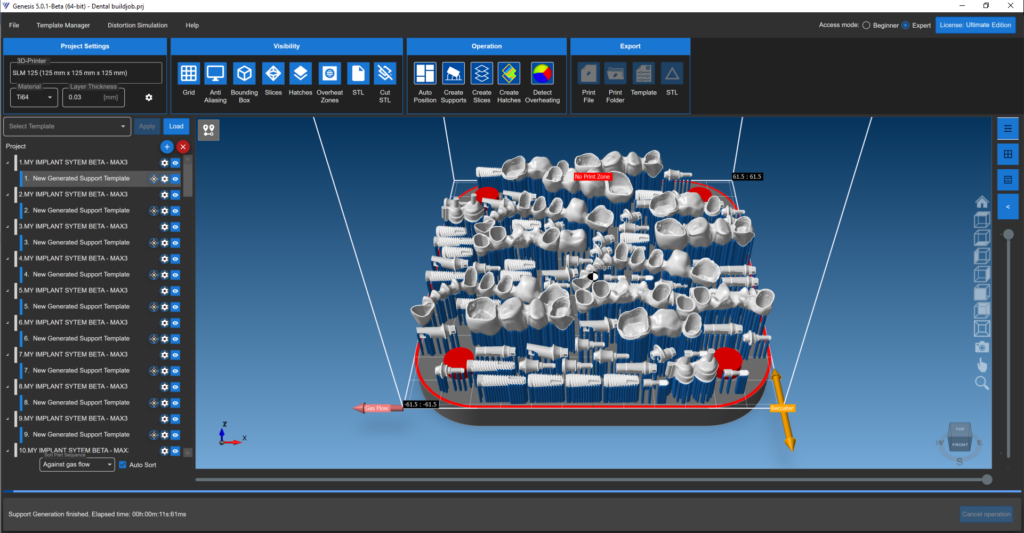
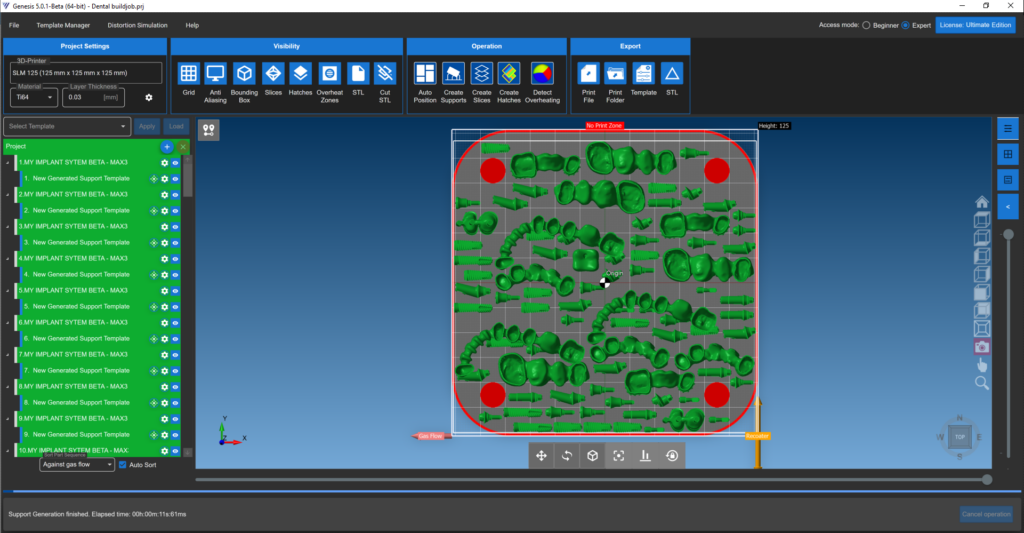
Support Generation
- Adjust the overhang angle and generate supports
- Customize parameters of your supports
- See real time visualization and make instant adjustments
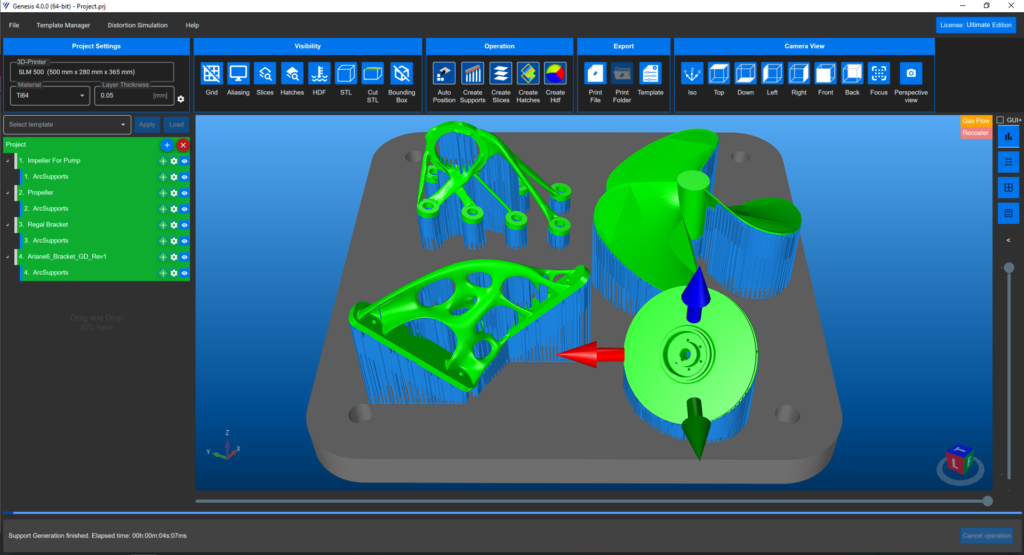
Slicing
- Fast & smart slicing
- Preview of every part contour
Standard Hatching
- Choose beetween following standard hatch patterns:
- Stripes hatch pattern
- Contour hatch pattern
- Unidirectional hatch pattern
- Checkerboard hatch pattner
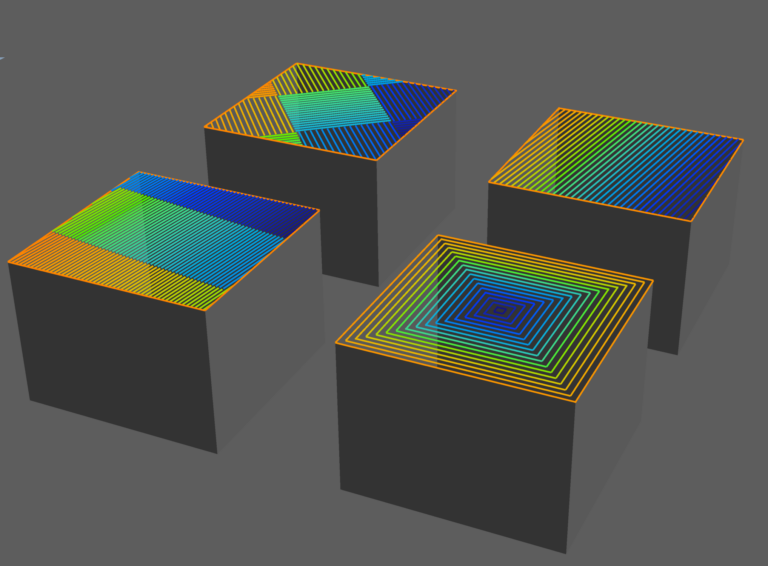
Generation of Artificial Defects
- Generate multi Hatching pattern within one layer to create artificial defects
- Define individual shapes and select the position
- Vary process parameter and hatching patterns for each artificial defect
- Excellent possibilities to calibrate monitoring systems
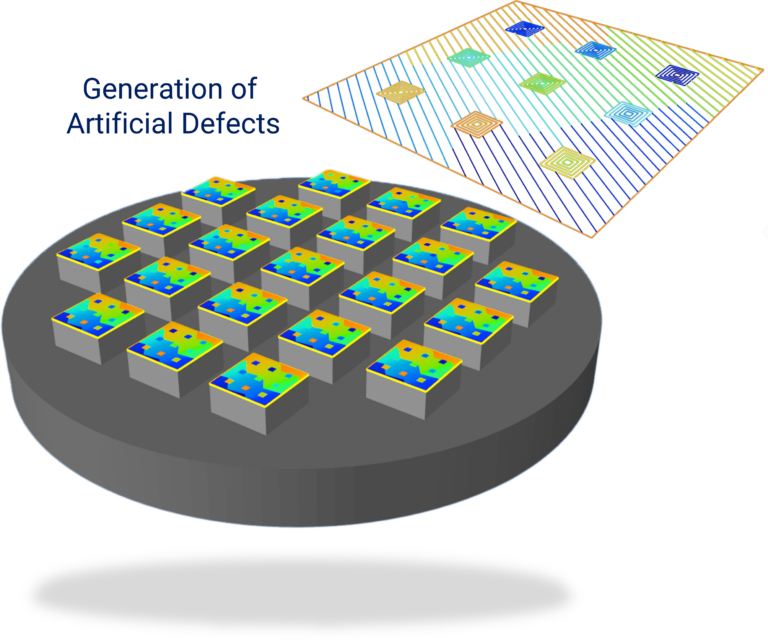
Layer Adjusted Hatching
- Define for each layer different hatching patterns and process parameters
- Excellent possibilities to calibrate new parameter sets
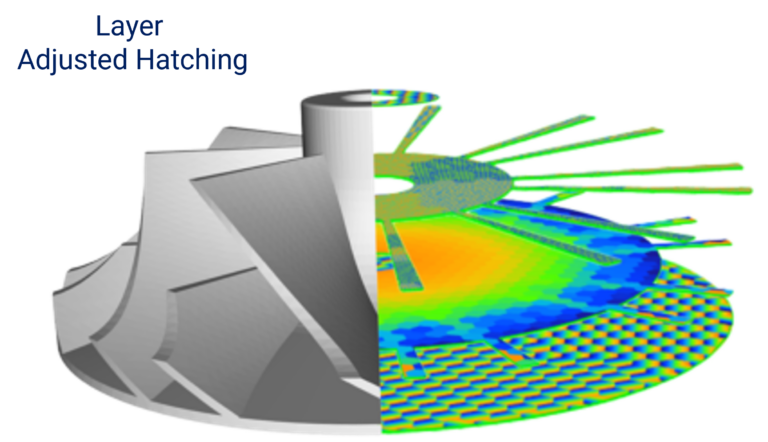
Export Print File
- Export your prepared buildjob easily in the proper printer format
In case, that your 3D-printer is not listed here, please contact us and correspond us the details of your printer-specific data format. We will quickly develop and provide you a data exporter, which will save the buildjob data in the format which matches for your 3D-printer
GENESIS API
For LB-PBF System Vendors
- Build-Processor as API package
- For integration into LB-PBF system software
- API package:
- Fast simulation of overheating
- Smart Hatching incl. parameter adaption
- Quick and easy integration
- .NET Framework
- C# program language
- Clear input and output documentation
- Technical support and debugging during implementation
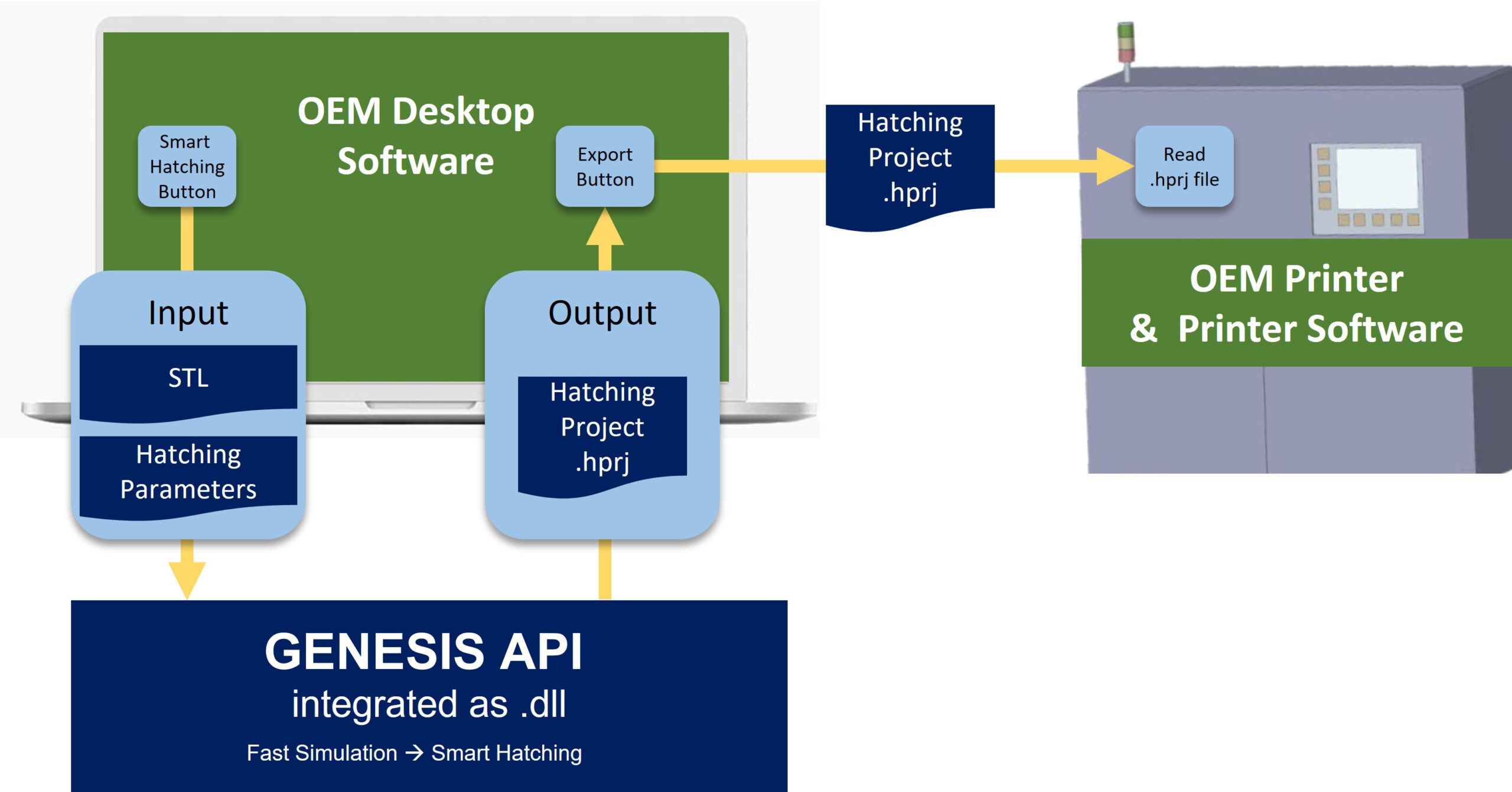